-
Stretch is a cell box-moving robotic, with a beefy arm and a big cell base.
-
The base is identical dimension as a pallet, so it could match anyplace a pallet matches.
-
Stretch’s additional arm joints let it attain the highest of the truck.
-
Stretch, in its compact folded-up mode.
After 28 years of analysis and improvement, Boston Dynamics entered the commercial robotic market final 12 months with the launch of Spot. This is a ~$75,000 robotic canine that may march round services for distant inspections and, with an additional arm attachment, may even open doorways and do distant manipulation.
Today, Boston Dynamics’ quest for commercialization continues with the announcement of a second commercial robotic, “Stretch,” a box-moving bot designed to satisfy the calls for of warehouses and distribution facilities. The robotic is designed to “go the place the work is” in a warehouse, unloading vehicles, de-palleting shipments, and ultimately constructing orders. For now, we’re seeing a prototype, however Boston Dynamics hopes firms will begin shopping for Stretch when it hits commercial deployment in 2022.
As Boston Dynamics VP of Product Engineering Kevin Blankespoor instructed us shortly earlier than the launch of Stretch, the corporate goes to the place the purchasers are. “When we launched our first Atlas “Next-gen” video,” Blankespoor stated, “there was part of that video that confirmed Atlas shifting bins, and we acquired an enormous response from individuals within the warehouse house. They wished Atlas to come back work at their warehouse.” Atlas is the corporate’s do-everything humanoid analysis robotic and might be far too costly to be a commercial product.
Blankespoor continues, “We thought, ‘Well, Atlas might be a bit sophisticated to truly go work in a warehouse, however we might design a robotic that is rather more easy that has the identical attributes.'” The consequence was not only a new robotic, however a complete warehouse-focused division inside Boston Dynamics, headed up by Blankespoor.
Getting a deal with on Stretch
With a transparent demand for warehouse robots, Boston Dynamics began experimenting, first with its “Handle” robotic. Handle began off life based mostly round a brand new “wheel-legged” mobility platform—that is two legs, however with wheels on the backside as a substitute of ft, enabling all kinds of nimble motion. The first model of Handle was a humanoid-ish robot that would do all types of loopy tips due to its wheel legs, like banking round corners, rolling down steps, and leaping onto a desk. The video reveals Handle lifting a field with its two humanoid arms, however the robotic wasn’t meant for warehouse work but.
For model 2, Handle was “re-imagined” from what appeared like a stunt robotic right into a warehouse robotic, and as a substitute of two arms, it used an enormous vacuum gripper to elevate bins. Handle nonetheless used the wheel-leg idea however now with an enormous counterweight on the again, and together with the lengthy “neck” that supported the vacuum gripper on the entrance, it regarded extra like a hen. Blankespoor says Handle might cowl quite a lot of Atlas-in-a-warehouse use instances however with one-third as many joints.
With Handle, Boston Dynamics acquired so far as doing experiments with prospects. The warehouse work proven within the Handle model 2 video confirmed the robotic loading and unloading a pallet in an enormous, open house, and Handle was good at that. The drawback with Handle is that generally warehouse work must occur in a confined house, like unloading a truck, and it was there that the robotic had issues.
Boston Dynamics / Ron Amadeo
“It turned clear that for Handle, maneuvering in a good house was tough,” Blankespoor defined. “We might do the job and get all of the bins unloaded, but it surely took too lengthy, principally. Every time Handle picked up a field, it needed to roll again to the center of the truck so it might rotate with out collisions, roll ahead, and place the field.” When lifting bins, Handle stored its steadiness with an enormous, swinging counterweight within the again, and it sounds just like the robotic’s large hen butt was continuously getting in the way in which. “We knew that there was this different possibility on the market,” Blankespoor stated. “We have been contemplating one thing like Stretch for years.”
Boston Dynamics
Stretch is the primary Boston Dynamics robotic that is “absolutely purpose-built” for the warehouse, and you may see that quite a lot of the nimble hen design has been thrown out in favor of an enormous, hulking industrial robotic. We’ll begin with the bottom: the robotic is solely mounted on an enormous field now, so it is steady by default and would not should actively steadiness anymore. The robotic weighs 2,650 lbs (1,200 kg) now, so there isn’t any want for an enormous, swinging counterweight when lifting—it isn’t going to tip over. The arm can spin round on prime of the bottom, so it could unload bins from a truck to a conveyor belt while not having to maneuver and stumble upon one thing. The result’s that Stretch can unload a truck about 5 occasions sooner than Handle. Stretch can transfer as much as 800 bins an hour.
Most warehouses are designed across the 48×40-inch dimensions of a pallet, so the bottom of Stretch simply occurs to have a 48×40-inch footprint, and it could match anyplace a pallet matches. Wheels in every nook of the field, all with impartial steering, let Stretch transfer in any course, together with aspect to aspect or rotating in place. The big base additionally means there may be quite a lot of room for the battery, sufficient to energy Stretch by an eight-hour work shift, or as much as 16 hours with “the prolonged vary possibility.”
Going to the place the work is
There are numerous stationary robotic arms that may transfer bins round, however fixed-infrastructure arms want pricey set up, and also you want one for each location the place a field must be moved. Being cell means Stretch can do the work of a number of stationary arms because the wants of the warehouse dictate, with out the necessity to redesign or set up something. Blankespoor imagines a typical day within the warehouse for Stretch: “Stretch would possibly spend the morning on the inbound aspect of the warehouse, unloading bins from vehicles. It would possibly spend the afternoon within the aisles of the warehouse, build up pallets—these will go off to retailers or e-commerce facilities. And it’d spend the night loading bins again into vehicles.”
Stationary arms could be as beefy as they must be, however being cell means Stretch wants to look at its weight. Boston Dynamics’ customized arm design is one-fourth the load of an industrial arm, whereas nonetheless with the ability to out-lift its predecessor, with a 50-pound max payload (23 kg) versus the 33-pound (15 kg) capability of Handle. The arm wanted to be designed so it might attain throughout pallets and bins all the way in which on the prime of the truck, the place there will not be a lot clearance. The robotic truly grabs the highest row of bins from the aspect, because it will not have the ability to match between the field and the roof.
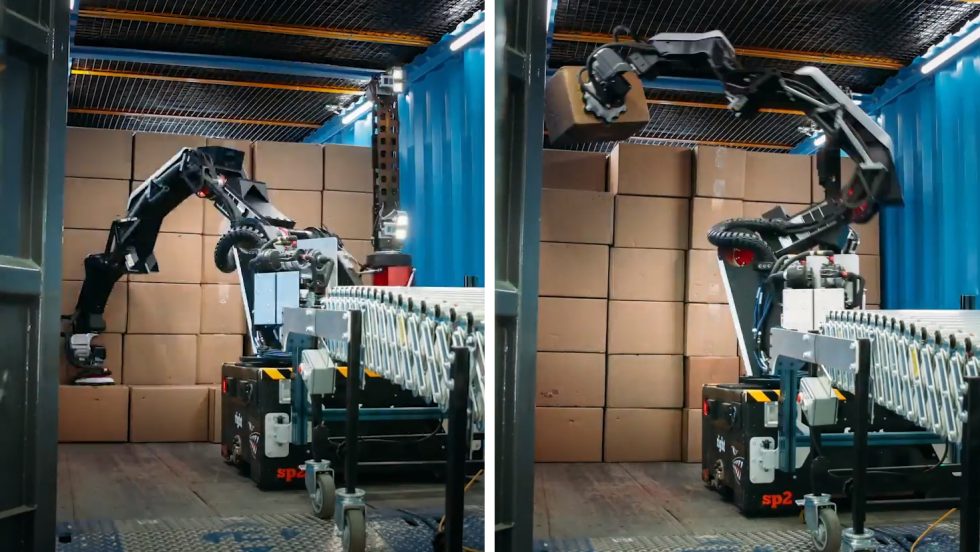
Boston Dynamics / Ron Amadeo
The remaining main part of Stretch is the notion mast, an enormous tower that sits on the identical rotating base because the arm and homes a lot of the robotic’s sensors, so it is by no means in the way in which of the arm. The mast homes each 2D and depth sensors, giving Stretch a high-up view of its environment. For imaginative and prescient, the robotic makes use of Boston Dynamics’ “Pick” software program, a set of machine-learning-powered algorithms for detecting and shifting bins, which arrived on the firm by way of an acquisition of Kinema Systems.
The base of Stretch truly has a modular interface the place you’ll be able to connect varied equipment. For truck unloading, you’ll be able to connect a conveyor belt to Stretch, so the robotic can deliver the conveyor belt with it because it strikes deeper into the truck. This means it solely ever has to simply choose up a field, spin round, and drop it for sooner unloading. There’s additionally a pallet cart attachment, so the robotic can haul a pallet round because it builds orders. Additional sensors could be connected to the bottom, too, both for situational consciousness like additional cameras or lidar, or a barcode reader for enter.
Boston Dynamics hopes to promote Stretch in 2022, but it surely nonetheless has some iteration to do earlier than then. What we’re seeing proper now’s the Stretch prototype, whereas the “product” model of Stretch can be bought someday next 12 months. As Blankespoor explains, “The Stretch product will look loads like this, but it surely’s actually been completely redesigned from the bottom up. Every part’s been reworked for manufacturability for value discount, reliability, and better efficiency. So the Stretch product, we are going to begin constructing the primary items of that this summer season, after which it’s going to go on sale next 12 months. We’ll begin rolling out functions that the product can do, incrementally. The first one we’ll do is truck unload, after which a bit bit later we’ll begin doing pallet constructing.” Blankespoor says the ultimate product will get a number of extra sensors, like a lidar on the face of the robotic.
“The different factor with the prototype is that our complete software program group will get a leap begin on creating management techniques, imaginative and prescient and autonomy, and testing it on actual {hardware},” Blankespoor tells us, “in order that once you get the product, the techniques are much more mature.”