The famous Pantheon in Rome boasts the world’s largest unreinforced concrete dome—an architectural marvel that has endured for millennia, thanks to the incredible durability of ancient Roman concrete. For decades, scientists have been trying to determine precisely what makes the material so durable. A new analysis of samples taken from the concrete walls of the Privernum archaeological site near Rome has yielded insights into those elusive manufacturing secrets. It seems the Romans employed “hot mixing” with quicklime, among other strategies, that gave the material self-healing functionality, according to a new paper published in the journal Science Advances.
As we’ve reported previously, like today’s Portland cement (a basic ingredient of modern concrete), ancient Roman concrete was basically a mix of a semi-liquid mortar and aggregate. Portland cement is typically made by heating limestone and clay (as well as sandstone, ash, chalk, and iron) in a kiln. The resulting clinker is then ground into a fine powder, with just a touch of added gypsum—the better to achieve a smooth, flat surface. But the aggregate used to make Roman concrete was made up of fist-sized pieces of stone or bricks.
In his treatise De architectura (circa 30 CE), the Roman architect and engineer Vitruvius wrote about how to build concrete walls for funerary structures that could endure for a long time without falling into ruins. He recommended the walls be at least two feet thick, made of either “squared red stone or of brick or lava laid in courses.” The brick or volcanic rock aggregate should be bound with mortar composed of hydrated lime and porous fragments of glass and crystals from volcanic eruptions (known as volcanic tephra).
Admir Masic, an environment engineer at MIT, has studied ancient Roman concrete for several years. For instance, in 2019, Masic and two colleagues (MIT’s Janille Maragh and Harvard’s James Weaver) pioneered a new set of tools for analyzing Roman concrete samples from Privernum at multiple length scales—notably Raman spectroscopy for chemical profiling and multi-detector energy dispersive spectroscopy (EDS) for phase mapping of the material.
Masic was also a co-author of a 2021 study analyzing samples of the ancient concrete used to build a 2,000-year-old mausoleum along the Appian Way in Rome known as the Tomb of Caecilia Metella, a noblewoman who lived in the first century CE. It’s widely considered one of the best-preserved monuments on the Appian Way. They used the Advanced Light Source to identify the many different minerals contained in the samples and their orientation, as well as scanning electron microscopy.
They discovered that the tomb’s mortar was similar to the walls of the Markets of Trajan: volcanic tephra from the Pozzolane Rosse pyroclastic flow, binding together large chunks of brick and lava aggregate. However, the tephra used in the tomb’s mortar contained much more potassium-rich leucite. The potassium in the mortar dissolved in turn and effectively reconfigured the binding phase. Some parts remained intact after more than 2,000 years, while other areas looked wispier and showed some signs of splitting. In fact, the structure somewhat resembled nanocrystals. So the interfacial zones constantly evolve through long-term remodeling, reinforcing those interfacial zones.
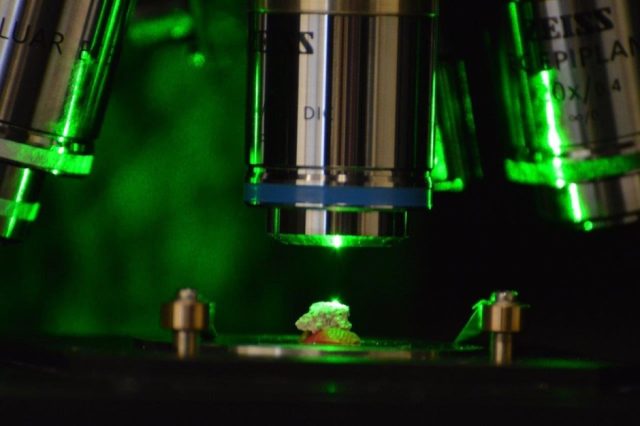
For this latest study, Masic wanted to take a closer look at strange white mineral chunks known as “lime clasts,” which others had largely dismissed as resulting from subpar raw materials or poor mixing. “The idea that the presence of these lime clasts was simply attributed to low quality control always bothered me,” said Masic. “If the Romans put so much effort into making an outstanding construction material, following all of the detailed recipes that had been optimized over the course of many centuries, why would they put so little effort into ensuring the production of a well-mixed final product? There has to be more to this story.”
It was believed that the Romans combined water with lime to make a highly chemically reactive paste (slaking), but this wouldn’t explain the lime clasts. Masic thought they might have used the even more reactive quicklime (possibly in combination with slaked lime), and his suspicion was born out by the lab’s analysis with chemical mapping and multi-scale imaging tools. The clasts were different forms of calcium carbonate, and spectroscopic analysis showed those clasts had formed at extremely high temperatures—aka hot mixing.
“The benefits of hot mixing are twofold,” Masic said. “First, when the overall concrete is heated to high temperatures, it allows chemistries that are not possible if you only used slaked lime, producing high-temperature-associated compounds that would not otherwise form. Second, this increased temperature significantly reduces curing and setting times since all the reactions are accelerated, allowing for much faster construction.”
It also seems to impart self-healing capabilities. Per Masic, when cracks begin to form in the concrete, they are more likely to move through the lime clasts. The clasts can then react with water, producing a solution saturated with calcium. That solution can either recrystallize as calcium carbonate to fill the cracks or react with the pozzolanic components to strengthen the composite material.
Masic et al. found evidence of calcite-filled cracks in other samples of Roman concrete, supporting their hypothesis. They also created concrete samples in the lab with a hot mixing process, using ancient and modern recipes, then deliberately cracked the samples and ran water through them. They found that the cracks in the samples made with hot-mixed quicklime healed completely within two weeks, while the cracks never healed in the samples without quicklime.
DOI: Science Advances, 2022. 10.1126/sciadv.add1602 (About DOIs).